PLC و اهمیت آن در صنعت
تاريخ :
۱۳۹۲/۱۱/۲۹
اهمیت PLC در صنعت
PLC، کنترل کننده ی نرم افزاری است که درقسمت ورودی، اطلاعاتی رابه صورت باینری دریافت وآن ها را طبق برنامه ای که درحافظه اش ذخیره شده پردازش می نماید ونتیجۀ عملیات را نیز از قسمت خروجی به صورت فرمان هایی به گیرنده ها واجرا کننده های فرمان (Actuators) ارسال می کند. به عبارت دیگر PLC عبارت از یک کنترل کنندۀ منطقی است که می توان منطق کنترل را توسط برنامه برای آن تعریف نمود و در صورت نیاز، به راحتی آن را تغییر داد.
وظیفۀ PLC بر عهدۀ مدارهای فرمان رله ای بود که استفاده از آنها در محیط های صنعتی جدید منسوخ گردیده است. اولین اشکالی که در این مدارها ظاهر می شود آن است که با افزایش تعداد رله ها حجم و وزن مدار فرمان، بسیار بزرگ شده، همچنین موجب افزایش قیمت آن می گردد. برای رفع این اشکال، مدارهای فرمان الکترونیکی ساخته شدند ولی با وجود این، هنگامی که تغییری در روند یا عملکرد ماشین صورت می گیرد مثلاً در یک دستگاه پرس، ابعاد، وزن، سختی و زمان قرار گرفتن قطعه زیر بازوی پرس تغییر می کند، لازم است تغییرات بسیاری در سخت افزار سیستم کنترل داده شود. به عبارت دیگر اتصالات و عناصر مدار فرمان باید تغییر کند.
کاربرد plc در تولید
با استفاده از PLC تغییر در روند تولید یا عملکرد ماشین به آسانی صورت می پذیرد، زیرا دیگر لازم نیست سیم کشی ها (Wiring) و سخت افزار سیستم کنترل تغییر کند و تنها کافی است چند سطر برنامه نوشت و به PLC ارسال کرد تا کنترل مورد نظر تحقق یابد.
از طرف دیگر قدرت PLC در انجام عملیات منطقی، محاسباتی، مقایسه ای و نگهداری اطلاعات به مراتب بیشتر از تابلوهای فرمان معمولی است. PLC به طراحان سیستم های کنترل این امکان را می دهد که آنچه را در ذهن دارند در اسرع وقت بیازمایند و به ارتقای محصول خود بیندیشند، کاری که در سیستم های قدیمی مستلزم صرف هزینه و به خصوص زمان است و نیاز به زمان، گاهی باعث می شود که ایدۀ مورد نظر هیچ گاه به مرحلۀ عمل در نیاید.
هر کس که با مدارهای فرمان الکتریکی رله ای کار کرده باشد به خوبی می داند که پس از طراحی یک تابلوی فرمان، چنانچه نکته ای از قلم افتاده باشد، مشکلات مختلفی ظهور نموده، هزینه ها واتلاف وقت بسیاری را به دنبال خواهد داشت. به علاوه گاهی افزایش و کاهش چند قطعه در تابلوی فرمان به دلایل مختلف مانند محدودیت فضا، عملاً غیر ممکن و یا مستلزم انجام سیم کشی های مجدد و پر هزینه می باشد.
اکنون برای توجه بیشتر به تفاوت ها و مزایای PLC نسبت به مدرات فرمان رله ای، مزایای مهم PLC را نسبت به مدارات یاد شده بر می شماریم:
استفاده از PLC موجب کاهش حجم تابلوی فرمان می گردد.
استفاده از PLC مخصوصاً در فرآیندهای عظیم موجب صرفه جویی قابل توجهی در هزینه، لوازم و قطعات می گردد.
- استهلاک مکانیکی ندارند، بنابراین علاوه بر عمر بیشتر، نیازی به تعمیرات و سرویس های دوره ای نخواهد داشت.
- انرژی کمتری مصرف می کند.
- بر خلاف مدارات رله کنتاکتوری، نویزهای الکتریکی و صوتی ایجاد نمی کنند.
استفاده از یک PLC منحصر به پروسه و فرآیند خاصی نیست و با تغییر برنامه می توان به آسانی از آن برای کنترل پروسه های دیگر استفاده نمود.
طراحی و اجرای مدارهای کنترل و فرمان با استفاده از PLC ها بسیار سریع و آسان است.
برای عیب یابی مدارات فرمان الکترومکانیکی، الگوریتم و منطق خاصی را نمی توان پیشنهاد نمود. این امر بیشتر تجربی بوده، بستگی به سابقۀ آشنایی فرد تعمیر کار با سیستم دارد. در صورتی که عیب یابی در مدارات فرمان کنترل شده توسط PLC به آسانی و با سرعت بیشتری انجام می گیرد.
PLC ها می توانند با استفاده از برنامه های مخصوص وجود نقص و اشکال در پروسۀ تحت کنترل را به سرعت تعیین و اعلام نمایند.
مزایای PLC نسبت به مدارات فرمان رله ای و همچنین مدارهای منطقی الکترونیکی و کامپیوتر بر شمرده شده است.
تفاوت PLC با کامپیوتر
استفاده از کامپیوتر معمولی مستلزم آموزش های نسبتاً طولانی، صرف وقت و هزینه های بسیاراست. چنانچه کنترل فرآیندی مورد نظر باشد استفاده از کامپیوتر معمولی به مراتب پیچیده تر و در اغلب موارد عملاً نا ممکن می شود. علاوه بر آن برای انطباق کامپیوتر با فرآیند مورد نظر، طراحی، ساخت و یا لااقل بررسی و خرید تجهیزات خاص برای انطباق، کاری طاقت فرسا است.
بسیاری از صنعتگران نیاز به کارگیری سیستم های اتوماتیک را عملاً احساس نموده و دریافته اند که تولید بدون به کارگیری اتوماسیون، اقتصادی نمی باشد. از طرف دیگر، صنعتگران آموزش های مبسوط به این شاخه از صنعت را در محدودۀ وظایف خود نمی دانند.
PLC وسیله ای است که درست به همین دلایل ساخته شده و اتوماسیون را با کمترین هزینه و به بهترین شکل ممکن در اختیار قرار می دهد. استفاده از PLC بسیار ساده بوده، نیاز به آموزش های مفصل، طولانی و پر هزینه ندارد.
از آنجائی که این وسیله به منظور پاسخگویی به کاربردهای صنعتی طراحی شده است، تمامی مسائل مربوط به آن حل شده، هیچ مشکلی در راه استفاده از آن وجود ندارد. طراحان خطوط تولید با بهره گیری از این وسیلۀ قابل انعطاف به سرعت می توانند نیازمندیهای مصرف کنندگان خود را تأمین و در اسرع وقت تواناییهای خود را با نیازمندی های بازار هماهنگ نمایند.
از شرکت های سازندۀ PLC می توان SIEMENS، AEG، BRADLEY ALLEN ، OMRON، MITSUBISHI و ... را نام برد. گر چه ازعرضۀ PLC توسط سازندگان مختلف چند ده سالی می گذرد و در ماشین آلات و خطوط تولید خریداری شده از خارج کشور نیز به وفور مشاهده می شود استفاده از این وسیلۀ بسیار قابل انعطاف توسط طراحان و ماشین سازان داخلی کمتر به چشم می خورد. از جمله عواملی که موجب تأخیر در بهره برداری از PLC توسط طراحان داخلی گردیده است عبارتند از:
- ارتباط مشکل با منابع تأمین کنندۀ خارجی.
- عدم دسترسی به موقع به اطلاعات سیستم ها.
- عدم پشتیبانی مؤثر سازندگان از تجهیزات فروخته شدۀ خود.
- هزینۀ بالای تجهیزات خارجی.
- هزینۀ بالای آموزش در خارج از کشور.
شرکت های داخلی نیز با توجه به مشکلات یاد شده و برای پر کردن خلاء موجود اقدام به طراحی و ساخت چند نوع PLC نموده اند. PLC های مذکور، کلیۀ امکانات استانداردهای PLC های متداول را داشته، از نمونه های خارجی با قابلیت های مشابه ارزانترند. این PLC ها به خوبی آزمایش گردیده، از پشتیبانی کامل آموزش و خدمات پس از فروش برخوردار می باشند.
از شرکت های داخلی تولید کنندۀ PLC و سیستم های اتوماسیون می توان شرکت کنترونیک را نام برد. این شرکت با به کارگیری دانش متخصصین داخلی اقدام به تولید چندین سیستم PLC با قابلیت های متفاوت جهت استفاده در صنایع مختلف و کاربردهای متنوع نموده است.
این شرکت همچنین مبتکر زبان برنامه نویسی خاصی جهت سیستم های PLC تولید شده می باشد که بسیار شبیه به زبان برنامه نویسی ابداع شده توسط شرکت SIEMENS یعنی STEP 5 است PLC یاد شده با نمونه های خارجی مشابه خود به خوبی رقابت می کند.
در فصول آینده با شبیه سازهای ابداع شده توسط این شرکت آشنا شده، روش برنامه نویسی را توسط این شبیه سازها مرور خواهیم نمود. گرچه در این کتاب سعی بر این است که سیستم PLC به طور کلی معرفی شود اما در مورد برنامه نویسی به ناچار باید از یک زبان برنامه نویسی خاص استفاه نماییم. امروزه کاربرد PLC های ساخت شرکت زیمنس در سر تا سر دنیا گسترش یافته، این نوع PLC بیش از هر PLC دیگری در صنایع مختلف به چشم می خورد. بنابراین مؤلف ترجیحاً از زبان برنامه نویسی STEP 5 (S5) که زبان برنامه نویسی سیستم های PLC زیمنس می باشد استفاده نموده است. همان گونه که گفته شد این زبان بسیار شبیه به زبان ابداع شده توسط شرکت کنترونیک یعنی CSTL بوده، و تفاوت این دو زبان برنامه نویسی تنها در چند مورد جزئی است. جهت آشنایی بیشتر خوانندگان با این زبان برنامه نویسی(CSTL) ، در برخی موارد سعی شده تا برنامۀ مورد نظر برای انجام یک پروسه به هر زبان S5 و CSTL نوشته شود تا خوانندگان شباهت های این دو زبان را بیشتر درک کنند.
لازم به ذکر است که اصول کلی زبانهای برنامه نویسی مختلف تقریباً یکسان بوده، خواننده می تواند با یادگیری یکی از زبانهای مذکور، سایر زبان ها را به آسانی درک و از آنها استفاده نماید.
سازندگان سیستم های PLC برای برنامه نویسی سیستم های خود، هر یک از زبان منحصر به فردی استفاده می نمایند که از نظر اصولی همگی تابع یک سری قوانین منطقی و کلی بوده، تنها تفاوت آنها در ساختار برنامه نویسی و نمادهای استفاده شده است.
از زبان های ابداع شده توسط سازندگان PLC می توان S5، FST، OMRON، CSTL، ALLEN BRADLEY و ... را نام برد.
کاربرد PLC در صنایع مختلف
امروزه کاربرد PLC در صنایع و پروسه های مختلف صنعتی به وفور به چشم می خورد، در زیر تعدادی از این کاربردها آورده شده است.
- صنایع اتومبیل سازی: عملیات سوراخ کاری اتوماتیک، اتصال قطعات و همچنین تست قطعات و تجهیزات اتومبیل، سیستم های رنگ پاش، شکل دادن بدنه به وسیلۀ پرس های اتوماتیک و ...
- صنایع پلاستیک سازی: ماشین های ذوب و قالب گیری تزریقی، دمش هوا و سیستم های تولید و آنالیز پلاستیک و ...
- صنایع سنگین: کوره های صنعتی، سیستم های کنترل دمای اتوماتیک، وسایل و تجهیزاتی که در ذوب فلزات استفاده می شوند و ...
- صنایع شیمیایی: سیستم های مخلوط کننده، دستگاههای ترکیب کنندۀ مواد با نسبت های متفاوت و ...
- صنایع غذایی: سیستم های سانتریفوژ، سیستم های عصاره گیری و بسته بندی و ...
- صنایع ماشینی: صنایع بسته بندی، صنایع چوب، سیستم های سوراخ کاری، سیستم های اعلام خطر و هشدار دهنده، سیستم های استفاده شده در جوش فلزات و ...
- خدمات ساختمانی: تکنولوژی بالابری (آسانسور)، کنترل هوا و تهویه مطبوع، سیستم های روشنایی خودکار و ...
- سیستم های حمل و نقل: جرثقیل ها، سیستم های نوار نقاله، تجهیزات حمل و نقل و ...
- صنایع تبدیل انرژی (برق، گاز و آب) شامل: ایستگاه های تقویت فشار گاز، ایستگاه های تولید نیرو، کنترل پمپ های آب، سیستم های تصفیۀ آب و هوای صنعتی، سیستم های تصفیه و بازیافت گاز و ...
سخت افزار PLC
از لحاظ سخت افزاری می توان قسمت های تشکیل دهندۀ یک سیستم PLC را به صورت زیر تقسیم نمود:
- واحد منبع تغذیه PS (Power Supply)
- واحد پردازش مرکزی CPU (Central Processing Unit)
- حافظه (Memory)
- ترمینال های ورودی (Input Module)
- ترمینال های خروجی (Output Module)
- مدول ارتباط پروسسوری CP (Communication Processor)
- مدول رابط IM (Interface Module)
- مدول منبع تغذیه (PS)
منبع تغذیه ولتاژهای مورد نیاز PLC را تأمین می کند. این منبع معمولاً از ولتاژهای 24 ولت DC و 110 یا 220 ولت AC، ولتاژ 5 ولت DC را مورد نیازCPU ومدول ها ایجاد می کند. ماکزیمم جریان قابل دسترسی منطبق با تعداد مدول های خروجی مصرفی است. لازم به ذکر است که ولتاژمنبع تغذیه باید کاملاً تنظیم شده (رگوله)[1] باشد.
جهت دستیابی به راندمان بالا معمولاً از منابع تغذیۀ سوئیچینگ استفاده می شود. ولتاژی که در اکثر PLCها استفاده می گردد ولتاژ 5 یا 2/5 ولت DC است. (در برخی موارد، منبع تغذیه و واحد کنترل شونده در فاصلۀ زیادی نسبت به یکدیگر قرار دارند. بنابراین ولتاژ منبع، 2/5 ولت انتخاب می شود تا افت ولتاژ حاصل از بُعد مسافت بین دو واحد مذکور جبران گردد.)
برای تغذیۀ رله ها و محرک ها (Actuator) معمولاً از ولتاژ 24 ولت DC به صورت مستقیم (بدون استفاده از هیچ کارت ارتباطی) استفاده می شود. در برخی موارد نیز از ولتاژ های 110 یا 220 ولت AC با استفاده از یک کارت به نام Relay Board استفاده می گردد. (در مورد: تغذیه رله ها احتیاج به رگولاسیون دقیق نیست.
دربرخی شرایط کنترلی لازم است تادرصورت قطع جریان منبع تغذیه اطلاعات موجود درحافظه و همچنین محتویات شمارنده ها، تایمرها وفلگ های پایدار (Retentive) بدون تغییر باقی بمانند. دراین موارد ازیک باطری جنس lithium جهت حفظ برنامه درحافظه استفاده می گردد. به این باطری "Battery back up" می گویند.
ولتاژ این نوع باطری معمولا ً 2.8 تا 3.6 ولت می باشد. ازآنجایی که این باطری نقش مهمی در حفظ اطلاعات موجوددرحافظه دارددراکثرplc ها یک چراغ نشان دهنده تعبیه شده ودرصورتی که ولتاژباطری به سطحی پایین ترازمقدارمجاز2.8 ولت برسداین نشان دهنده روشن می گردد. این نشان دهنده به Battery Low LED معروف است .درصورت مشاهده ی روشن شدن این نشان دهنده لازم است که باطری مذکور تعویض گردد. برای تعویض باطری ابتدا باید به وسیله ی یک منبع تغذیه، ولتاژمدول مورد نظررا تامین وسپس اقدام به تعویض باطری نمود .
واحد پرازش مرکزی (cpu)
CPU یاواحد پردازش مرکزی درحقیقت قلب PLC است. وظیفه ی این واحد، دریافت اطلاعات ازوودی ها، پردازش این اطلاعات مطابق دستورات برنامه وصدور فرمان هایی است که به صورت فعال یا غیر فعال نمودن خروجی ها ظاهر می شود. واضح است که هرچه سرعت پردازش CPU بالاتر باشدزمان اجرای برنامه کمتر خواهد بود.
حافظه (memory)
همان گونه که می دانید حافظه محلی است که اطلاعات و برنامه ی کنترل در آن ذخیره می شود. علاوه بر این، سیستم عامل 2 که عهده دار مدیریت کلی در PLC است درحافظه قرار دارد. تمایز درعملکرد PLC ها، عمدتاً به دلیل برنامه ی سیستم عامل و طراحی خواصCPU آن هاست. درحالت کلی در PLCها دو نوع حافظه وجود دارد:
حافظه ی موقت (RAM): که شامل نگهداری فلگ ها، تایمر ها، شمارنده ها و برنامه های کاربراست.
حافظه دائم (EPROM, EEPROM): که جهت نگهداری وذخیره همیشگی برنامه کاربر1 استفاده می گردد.
ترمینال ورودی INPUT MODULE))
این واحد، محل دریافت اطلاعات از فرایند یاپروسه ی تحت کنترل می باشد. تعداد ورودی هادرPLC های مختلف، متفاوت است. ورودی هایی که در سیستم های PLC مورد استفاده قرار می گیرند در حالت کلی به دو صورت زیر می باشند:
- ورودی های دیجیتال (DIGITAL INPUT)
- ورودی های آنالوگ (ANALOG INPUT)
ورودی های دیجیتال یا گسسته
این ورودی ها معمولا به صورت سیگنال های صفر یا 24 ولت DC می باشند، گاهی برای پردازش توسط CPU به تغییر سطح ولتاژ نیاز دارند. معمولاً برای انجام این عمل مدول هایی خاص در PLC در نظر گرفته می شود.
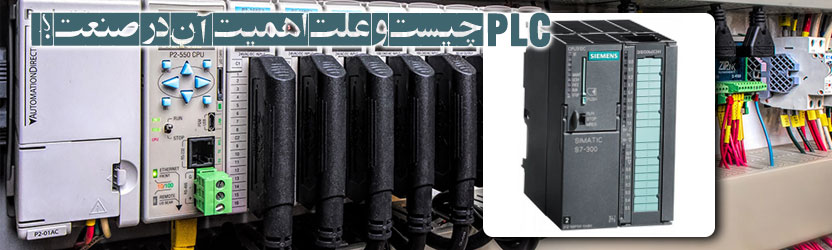
جهت حفاظت مدارات داخلی PLC از خطر ناشی از اشکالات بوجود آمده در مدار یا برای جلوگیری از ورود نویز های موجود در محیط های صنعتی ارتباط ورودی ها با مدارات داخل PLC توسط کوپل کننده های نوری (Optical Coupler) انجام می گیرد. به دلیل ایزوله شدن ورودی ها از بقیه ی اجزای مدار داخلی PLC، هرگونه اتصال کوتاه و یا اضافه ولتاژ نمی تواند آسیبی به واحد های داخلی PLC وارد آورد.
ورودی های آنالوگ یا پیوسته
اینگونه ورودی ها در حالت استاندارد V DC10 ± - 0 ،mA 20- 4 و یا mA 20 - 0 بوده، مستقیما به مدول های آنالوگ متتصل می شوند. مدول های ورودی آنالوگ سیگنال های دریافتی پیوسته (آنالوگ) را به مقادیر دیجیتال تبدیل نموده، سپس مقادیر دیجیتال حاصل توسط CPU پردازش می شوند.
ترمینال خروجی (Output Module)
این واحد محل صدور فرمان های PLC به پروسه ی تحت کنترل می باشد . تعداد این خروجی ها در PLC های مختلف متفاوت است. خروجی های استفاده شده درPLCها به دو صورت زیروجود دارند:
- خروجی های دیجیتال (Digital Output)
- خروجی های آنالوگ (Analog Output)
خروجی های دیجیتال یا گسسته
این فرمانهای خروجی به صورت سیگنال های 0 یا 24 ولت DC بوده که در خروجی ظاهر می شوند، بنابراین هر خروجی از لحاظ منطقی می تواند مقادیر "0" (غیر فعال ) یا "1" (فعال ) را داشته باشد این سیگنال ها به تقویت کننده های قدرت یا مبدل های الکتریکی ارسال می شوند تا مثلاً ماشینی را به حرکت در آورده ( فعال نمایند ) یا آن را از حرکت باز دارند (غیر فعال نمایند). در برخی موارد استفاده از مدول های خروجی دیجیتال جهت رسانیدن سطوح سیگنال های داخلی PLC به سطح 0 تا 24 ولت DC الزامی است .
خروجی های آنالوگ یا پیوسته
سطوح ولتاژ و جریان استاندارد خروجی میتواند یکی از مقادیر DC V 10± - 0 ،mA 20-4 ویا mA 20-0 باشد. معمولاً مدول های خروجی آنالوگ مقادیر دیجیتال پردازش شده توسط CPU را به سیگنالهای یوسته (آنالوگ ) مورد نیاز جهت پروسه ی تحت کنترل تبدیل می نمایند. این خروجی ها به وسیله ی واحدی به نام Isolator از سایر قسمت های داخلی PLC ایزوله می شوند .بدین ترتیب مدارات حساس داخلی PLC ازخطرات ناشی از امکان بروز اتصالات ناخواسته ی خارجی محافظت می گردند.
مدول ارتباط پروسسوری (cp)
این مدول، ارتباط بین CPU مرکزی را با CPU های جانبی (جهت شبکه شدن) برقرار می سازد.
مدول رابط (IM)
در صورت نیاز به اضافه نمودن واحد های دیگر ورودی وخروجی به PLC یاجهت اتصال پانل اپراتوری وپروگرامر به PLC از این مدول ارتباطی استفاده می شود (بعبارتی جهت توسعه PLC). د رصورتی که چندین PLC به صورت شبکه به یکدیگر متصل می شوند از واحد IM جهت ارتباط آنها استفاده می شود.
تصویر ورودی ها
قبل از اجرای برنامه، CPU وضعیت تمام ورودی ها را بررسی و در قسمتی از حافظه به نام PII نگهداری می نماید. جز در موارد استثنایی و تنها در بعضی از انواع PLC، غالباً در حین اجرای برنامه، CPU به ورودی ها مراجعه نمی کند بلکه برای اطلاع از وضعیت هر ورودی به سلول مورد نظر در PII رجوع می کند. در برخی ازPLCها این قسمت از حافظه، IIT (Input Image Table) نیز خوانده می شود.
تصویر خروجی ها
هر گاه در حین اجرای برنامه یک مقدار خروجی بدست آید، در این قسمت از حافظه نگهداری می شود. جز در موارد استثنایی و تنها در برخی از انواع PLC، غالباً در حین اجرای برنامه، CPU به خروجی ها مراجعه نمی کند بلکه برای ثبت آخرین وضعیت هر خروجی به سلول مورد نظر در PIO رجوع می کند و در پایان اجرای برنامه، آخرین وضعیت خروجی ها از PIO به خروجی های فیزیکی منتقل می گردند. در برخی موارد این قسمت از حافظه را OIT (Output Image Table) نیز می گویند.
- Internal program memory (RAM)
- CPU Memory submodule) (EPROM / EEPROM / RAM)
- ACCUM
- Processor
- Timers, counters, flags
- Serial interface
- PII
- PIO
- I /O bus
- Output modules (digital/analog)
- Input modules (digital/analog)
- Functional modules
- Input /Output modules
فلگ ها، تایمر ها و شمارنده ها
هر CPU جهت اجرای برنامه های کنترلی از تعدادی تایمر، فلگ و شمارنده استفاده می کند. فلگ ها محل هایی از حافظه اند که جهت نگهداری وضعیت برخی نتایج و یا خروجی ها استفاده می شوند.
جهت شمارش از شمارنده و برای زمان سنجی از تایمر استفاده می گردد. فلگ ها، تایمر ها و شمارنده ها را از لحاظ پایداری و حفظ اطلاعات ذخیره شده می توان به دو دستۀ کلی تقسیم نمود:
پایدار (Retentive):به آن دسته از فلگ ها، تایمر ها و شمارنده هایی اطلاق می گردد که در صورت قطع جریان الکتریکی (منبع تغذیه) اطلاعات خود را از دست ندهند.
ناپایدار (Non - Retentive) این دسته بر خلاف عناصر پایدار، در صورت قطع جریان الکتریکی تغذیه، اطلاعات خود را از دست می دهند.
تعداد فلگ ها، تایمر و شمارنده ها در PLC های مختلف متفاوت می باشد اما تقریباً در تمامی موارد قاعده ای کلی جهت تشخیص عناصر پایدار و ناپایدار وجود دارد.
فرض کنید که در یک نوع PLC خاص تعداد تعداد فلگ ها، تایمر ها و شمارنده ها به ترتیب m و n و p باشد. تعداد عناصر پایدار و ناپایدار با یکدیگر برابر است. بنابراین تعداد این عناصر به ترتیب می باشد. المان های که شمارۀ آنها از مقادیر نصف یعنی کوچکتر باشد پایدار و بقیه، عناصر ناپایدار هستند. به طور کلی می توان گفت که نیمۀ اول این عناصر، پایدار و نیمۀ دوم ناپایدار می باشد.
فرض کنید که در یک نوع PLC، 16 شمارنده (C0– C 15) تعریف شده باشد بنا بر قاعدۀ مذکور شمارنده های C0 – C7 همگی پایدار و شمارنده های C8 – C 15 ناپایدار می باشند.
انبارک یا آکومولاتور (ACCUM)
انبارک یا آکومولاتور یک ثبات منطقی است که جهت بارگذاری یا به عبارت دیگر لود نمودن اطلاعات استفاده می گردد. از این ثبات جهت بارگذاری اعداد ثابت در تایمرها، شمارنده ها، مقایسه گرها و ... استفاده می شود.
گذر گاه عمومی ورودی / خروجی ( I /O bus)
همان گونه که قبلاً ذکر شد وظیفۀ پردازش اطلاعات در PLC بر عهدۀ CPU است. بنابراین برای اجرای برنامه بایستی CPU با ورودی ها، خروجی ها و سایر قسمتهای PLC در ارتباط بوده، با آنها تبادل اطلاعات داشته باشد. سیستمی که مرتبط کنندۀ CPU با قسمتهای دیگر است bus نامیده می شود. این سیستم توسط CPU اداره می شود و در حقیقت علت کاهش چشمگیر اتصالات در PLC به دلیل وجود همین سیستم می باشد. سیستم bus از سه بخش زیر تشکیل شده است.
- باس داده (Data bus)
- باس آدرس (Address bus)
- باس کنترل (Control bus)
مشخصات سیستم باس بستگی به نوع CPU مورد استفاده و حجم کلی حافظه دارد. مثلاً پردازشگر Z80 باس داده دارای 8 خط ارتباطی است که ارسال و دریافت هشت بیت یا یک بایت اطلاعات را امکان پذیر می سازد. بنابراین ورودی ها، خروجی ها و حافظه ها بایستی در دسته های هشت بیتی یا یک بایتی سازماندهی شوند.
هر بایت اطلاعات بایستی آدرس منحصر به فردی داشته باشد، هر گاه CPU بخواهد اطلاعاتی با بایت بخصوص رد و بدل نماید با استفاده از آدرس منحصر به فرد آن بایت این تبادل اطلاعات امکان پذیر می گردد. وقتی تمام امکانات CPU با بایت مورد نظر از لحاظ آدرس و خط ارتباطی فراهم شد CPU توسط باس کنترل، جهت حرکت و زمان رد و بدل اطلاعات را سازماندهی می کند.
روش های مختلف آدرس دهی
جهت آدرس دهی معمولاً از سه روش زیر استفاده می شود.
- (Fixed Address): در این روش تمام ورودی ها و خروجی ها دارای آدرس ثابتی باشند. نظیر این نوع آدرس دهی را در مینی PLC های کنترونیک یارله های قابل برنامه ریزی زیمنس (LOGO) می توان یافت.
- (Slot Address): در این روش، آدرس دهی قابل تغییر می باشد و این تغییر آدرس توسط شیارهای مورد نظر و فیش های زائده دار انجام می گیرد.
- (Flexible Address): در این روش آدرس دهی که قابل تغییر نیز می باشد سوئیچ هایی (دیپ سوئیچ) در نظر گرفته شده که با استفاده از آنها می توان آدرس دهی را تغییر داد.
حال که با سخت افزار سیستم های PLC آشنا شدیم به بررسی نرم افزار آن می پردازیم.
نرم افزار PLC
در PLC ها سه نوع نرم افزار قابل تعریف است: نرم فزاری که کارخانۀ سازنده با توجه به توان سخت افزاری سیستم تعریف می کند که به آن Operating System یا به اختصار OS گویند. مثلاً در PLC زیمنس مدل 100 U تعداد 16 تایمر ( T0 – T15) تعریف شده است و اگر در برنامه نویسی از تایمر شمارۀ 18 استفاده می شود. سیستم عامل دستور مذکور را به عنوان یک دستور اشتباه قلمداد کرده، برنامه اجراء نخواهد شد.
لازم به ذکر است که این نرم افزار ثابت بوده ، قابل تغییر نمی باشد بنا براین ازنوع فقط خواندنی است و معمولاً در EPROM یا E2PROM ذخیره می شود.
نرم افزاری که برنامه نوشته شده توسط استفاده کننده (user) را به زبان قابل فهم ماشین تبدیل می نماید. این برنامه منحصر به کارخانه سازنده بوده، نام خاصی نیز دارد. معروفترین وپرکاربرد ترین درPLC زیمنس این نرم افزار ها S5 وs7 می باشد که توسط شرکت زیمنس ابداع گردیده است. این نرم افزار همانند OS قابل تغییر نیست و بایستی در ROM ذخیره گردد وبرای اجرا به RAM پروگرامر ارسال گردد.
نرم افزار یا برنامه ای که توسط استفاده کننده نوشته می شود و به آن User Program می گویند. این نرم افزار درهرلحظه قابل تغییر بوده، خواندنی ونوشتنی است. این نرم افزار درRAM و یا در EPROM و یا در E2PROM ذخیره و در صورت لزوم از مدول ذکر شده مجدداً در RAM کپی شده، اجرا می گردد.
همانگونه که ذکر شد هر PLC شامل سخت افزار و نرم افزار می باشد. درصفحات گذشته به طور اجمال به توضیح در موردسیستم های سخت افزاری وهمچنین نرم افزار PLC پرداختیم. واضح است که برای وارد کردن برنامه ی کنترلی یا نرم افزاری به سخت افزار ، نیاز به یک واحدبرنامه نویس یا پروگرامر می باشد . در ادامه ی بحث به واحد تشریح واحد برنامه نویسی (Programming Unit) می پردازیم.
واحد برنامه نویسی (PG)
در استفاده وبه کارگیری PLC علاوه بر آشنایی با نحوه ی کار، آشنایی با واحد برنامه نویسی آن نیز ضروری است زیرا توسط این واحد قادر خواهیم بود با PLC ارتباط بر قرار نماییم. به این ترتیب که برنامه ی کنترل دستگاه را نوشته، آن را در حافظه ی PLC قرار داده، اجرای آن را از PLC می خواهیم. این واحد بسیار شبیه به کامپیوترهای معمولی است، یعنی دارای یک صفحه ی نشان دهنده (مونیتور) وصفحه کلید می باشد. تفاوت PG با کامپیوتر معمولی، تک منظوره بودن آن می باشد بدین معنی که از PG تنها می توان جهت ارتباط برقرار نمودن با PLC مربوطه استفاده نمود.
با استفاده از PG می توان از وضعیت وچگونگی اجرای برنامه مطلع شد. صفحه ی نمایش واحد برنامه نویسی به ما نشان می دهد که کدام ورودی روشن یا خاموش است، PLC توسط خروجی ها دستور فعال شدن یا توقف کار کدام ماشین را می دهد ودرحقیقت نحوه ی اجرای برنامه در صفحه ی نمایش ظاهر می شود. بنا بر این در صورتی که اشکال در برنامه وجود داشته باشد یا ایرادی در اجرای برنامه پیدا شود، از این طریق می توان به آن پی برد. پس می توان گفت گه واحد برنا مه نویسی در عیب یابی برنامه ی کنترل دستگاه ها و سیستم های تحت کنترل و بررسی علت توقف آن ها نقش بسزایی دارد. به وسیله ی PG می توان تغییرات عملوندها یعنی ورودی ها ،خروجی ها و همچنین تایمر ها و شمارنده های برنامه ی در حال اجرا رابه صورت Real Time ملاحظه نمود. در اکثر PLC ها به کمک PG می توان با دستو خاصی نظیر STATUS وضعیت عملوند ها را در حین اجرای برنامه مشاهده نمود.